The company manufactures high-quality tube couplings, adaptors, pipe flanges, diagnostic couplings, and allied control valves under the brand name Hyloc for more than 50+ years.
10 Tips for Safe and Reliable Hydraulic Plumbing
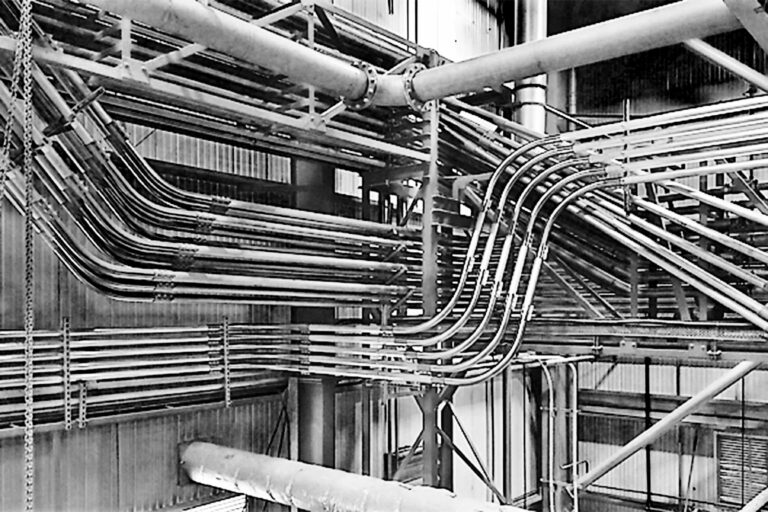
When it comes to creating good hydraulic plumbing systems, there are several key tips to keep in mind. Here are ten tips by hyloc to help you make the most of your hydraulic plumbing:
- Plan and design the system carefully: Before starting any plumbing work, take the time to plan and design the system thoroughly. Consider the specific requirements, layout, flow rates, pressure limits, and any potential issues that may arise.
- Select the right components: Choose high-quality hydraulic components that are suitable for the intended application. Ensure that the tube fittings, adaptors, hoses, valves and pumps meet the necessary specifications and standards.
- Use proper tube fittings and connectors: Select appropriate tube fittings and connectors that provide reliable connections and prevent leaks. Use the correct type and size of fittings for the specific hydraulic hoses and pipes you are using.
- Pay attention to tube/hose routing: Proper tube or hose routing is crucial for optimal hydraulic performance. Avoid sharp bends, kinks, or tight bends that can restrict flow and cause pressure drops. Use clamps and supports to secure the tubes or hoses and prevent chafing or damage.
- Ensure proper sealing: Achieving effective sealing is vital to prevent leaks and maintain system integrity. Use quality seals, O-rings, and gaskets that are compatible with the hydraulic fluids being used. Apply the appropriate sealing techniques and follow manufacturer guidelines.
- Avoid excessive hose length: Keep the length of hydraulic hoses to a minimum to minimize pressure losses. Long hoses can increase friction losses and reduce overall system efficiency. Use the shortest hose length possible while still allowing for movement and flexibility.
- Follow recommended torque specifications: Properly tighten all tube fittings and connectors to the manufacturer’s recommended assembly guidelines or torque specifications. Under-tightened connections can lead to leaks, while over-tightened fittings may cause damage or stripping.
- Purge air from the system: Prior to commissioning the hydraulic system, ensure that all air is purged from the system. Air trapped within the system can cause performance issues, such as spongy or inconsistent response, and can lead to damage in the long run.
- Test for leaks and pressure: After installation, conduct thorough leak testing and pressure testing to verify the integrity of the system. Monitor for any signs of leaks or pressure drops and address them promptly.
- Regular maintenance and inspection: Establish a maintenance schedule for your hydraulic plumbing system and perform regular inspections. Check for any signs of wear, leaks, or damaged components. Maintain proper fluid levels and cleanliness, and replace any worn-out parts promptly.